
TSA Surface Preparation and Application
The most important concept of this document is that in order to achieve a successful thermal sprayed aluminum or zinc coating (TSA), the surface being sprayed must be clean, dry, and freshly blasted. Both the performance and the adhesive strength of a TSA coating is entirely dependent upon the coating locking itself into the pores of the substrate surface with no interference from any contaminant that would cause a lack of electrical conductivity or reduce the bond strength. With this principle in mind, the following steps will help achieve the best quality coating:
Pre-Surface Preparation
It is important that a visual inspection for defects be conducted prior to the start of surface preparation. Prior to blasting, any weld defects, spatter, pits, crevices, fatigued metal, or sharp angles should be removed by disc grinding or some other mechanical method. As a rule, thermal spray coatings do not adhere well to sharp right angled edges. The slight shrinkage that occurs during the cooling process tend to create a stress point at these edges which sometimes causes the coating to lift along the edge. It’s always best to round off corners prior to blasting.
The surface to be blasted should be clean and free of any oil, grease, inspection fluids, or any other hydrocarbon type contaminants. Solvent clean in accordance with SSPC-SP 1 to remove such contaminants prior to blasting. Once the surface has been blasted, do not use cleaning solutions, rust inhibitors, or any solvent that would leave a residue on the surface to be coated. Any such product could be easily trapped in the surface pores of the metal, greatly reducing bond strength.
All non-destructive testing of welds etc. should be completed prior to blasting and coating so as to minimize surface contamination.
Surface Preparation
TSA coatings form a “mechanical bond” on the surface of another metal similar to solders, paints, and epoxies. The molten metal is driven into the surface pores of the substrate metal where it solidifies and locks itself into place. The strength of the bond depends on surface cleanliness, depth of profile, temperature of the work piece, and the angle or distance of the spray stream. It is important that any surface to be coated be blast cleaned to SSPC-SP5, ISO 8501-1 (white metal blast) and exhibit the proper profile.
Compressed air used for blasting and spraying should be free of oil and moisture as either of these two contaminants will affect bond strength. Before each shift a “blotter” test should be performed on the compressed air source in accordance with ASTM D4285-88 to ensure the air source is free of contaminants. Use filters, dryers, separators and traps as necessary between the air source and the flow meters to remove any moisture etc. Blast nozzles and hoses that are worn should be replaced. Most customers will require you to document the results of your preliminary tests and replace or repair any faulty equipment.
Ambient conditions should be checked and documented prior to any blasting or thermal spray coating begins. Blasting should not be performed when the surface to be blasted is wet or when the surface is less than 5oF (3oC) above the dew point temperature.
Abrasive Blasting
The blast nozzle, air pressure, and all related equipment should be inspected to insure they are within specification and in good working order prior to each shift. Appropriate personal protection gear should be worn when performing any abrasive blast operation.
Suitable abrasive media for obtaining the proper anchor profile for thermal spray are 10 to 30 grit aluminum oxide, Garnet (GH-16 to GH-40, Angular Steel Grit (GH-16 to GH-40) or Chilled Iron Grit (GH-16 to GH-40). Never use silica sands, as this media tends to fracture and imbed shards of silica in the pores of the metal which interfere with the bond and electrical conductivity. Inspect blast media prior to use to insure it is clean, dry, sharp, and free of any contaminants in accordance with ASTM D 4940. Visually inspect the media for any oil or contaminants. A small amount of the media can be placed in a clean container of water and shaken. Look for any floating debris or oil film. Again, it is always a good idea to document your inspections just in case there is ever an issue with bond failure.
The required anchor profile depth for thermal spray aluminum coatings is 3 to 6 mils (slightly less for zinc). This profile is determined on representative sample coupons (which you will need for bond strength testing later) or on the work piece itself using Testex Press-o-film X-Coarse Replica Tape or an approved equivalent and Surface Profile Comparator in accordance with ISO 8503-5 and ISO 8503-2 or ASTM D4417 Methods A and C. If the desired profile is not met, change the air pressure or blast media until the proper profile is achieved. Profile measurements should be taken every 10 m2. Again, document your test results.
Once blasting is performed, inspect once again for any missed areas, sharp corners, fatigued metals, etc. The surface should not be touched with dirty hands or rags from this point forward. If the surface is accidentally contaminated, small areas may be cleaned with a top quality residue free degreaser such as Metalink® MetalPrep II ™ Degreaser. Thermal spray coating should commence within 6 hours of completion of blasting. It is always a good idea to blast no more surface than can be reasonably coated during the same shift or the following shift. In certain arid climates this time frame may be extended slightly, especially when spraying on hot process towers or piping where there is no chance of condensation or surface oxides forming. When blasting tall vertical surfaces, it is best to start at the top and work down so that thermal spray coatings may be applied afterwards without having to blow off contaminants.
In areas where abrasive blasting cannot be reasonably performed, proper cleaning and surface profiling may be achieved through mechanical means. A right angle grinder with a good quality 40grit zirconia flap disc will typically achieve a suitable profile. Special power brushes that are bent to produce an impact on the surface of the metal (such as a Bristle-Blaster® Power Tool) will produce a surface that most closely approximates grit blasting. These methods are commonly employed in operating units for coating welds of piping that have previously been TSA coated or areas that simply cannot be reached by blasting. In either case, preheats of 125 to 150oF will help increase bond strengths.
Finally, be sure to mask off any areas where spray deposit is not desired. Brushable masking compound (such as Metalink® Masking Compound) is suitable for this application, as well as numerous thermal spray masking tapes.
Application of Coatings
Before using any thermal spray equipment, you must be thoroughly familiar with the manufacturers operating and safety instructions for whichever application method you employ (combustion or twin wire arc). TSA contractors are usually required to be certified in their proficiency by the manufacturer of the equipment prior to actual job site application. Before each shift begins, perform all recommended equipment and gas flow inspections and safety checks. Compressed air should be free of oil and condensed moisture (see compressed air requirements above). Your application equipment should be capable of a minimum of twenty to thirty minute uninterrupted spray intervals in order to be most efficient.
Proper personal protection equipment or “PPE” should be worn according to job site requirements and available ventilation. Any Hot Work Permits or Confined Space Work Permits should be obtained from the owner’s administrator prior to any work being performed.
The surface temperature of the object to be coated should be at least 30 C above the dew point. If pre-heating is used to eliminate any surface moisture, the heating method should be clean and not deposit any contaminates on the surface. Pre-heat should not exceed 650 C. If using the combustion gun process, only a small surface area would ever be required to be pre-heated, as the flame from the gun will warm up adjacent areas once work commences. Pre-heat is not necessary at all with the twin wire arc process.
Materials
When spraying aluminum coatings, the wire should be top quality spooled or coiled alloys conforming to ISO 209-1, AWS C2.25/C2.25M or ASTM B 833 grades 1100 (99% pure) or 1350 (99.5% pure) depending on the application requirements. The wire should be individually wrapped or boxed and exhibit the manufacturer’s label and lot number. Material certifications should be kept on hand to match with the appropriate lot numbers for complete traceability. Keep accurate records of all lot numbers used on any particular job. Great care should be given to ensure that wire inventories remain contaminant and blemish free in order to ensure maximum productivity. Even the smallest surface abrasions may interfere with the way the wire feeds through the gun. Keep in mind that the term “TSA” has become somewhat of a generic industrial term that could also encompass the use of Zinc and Zinc/Aluminum alloys as well. All the same precautions apply to the use of these materials.
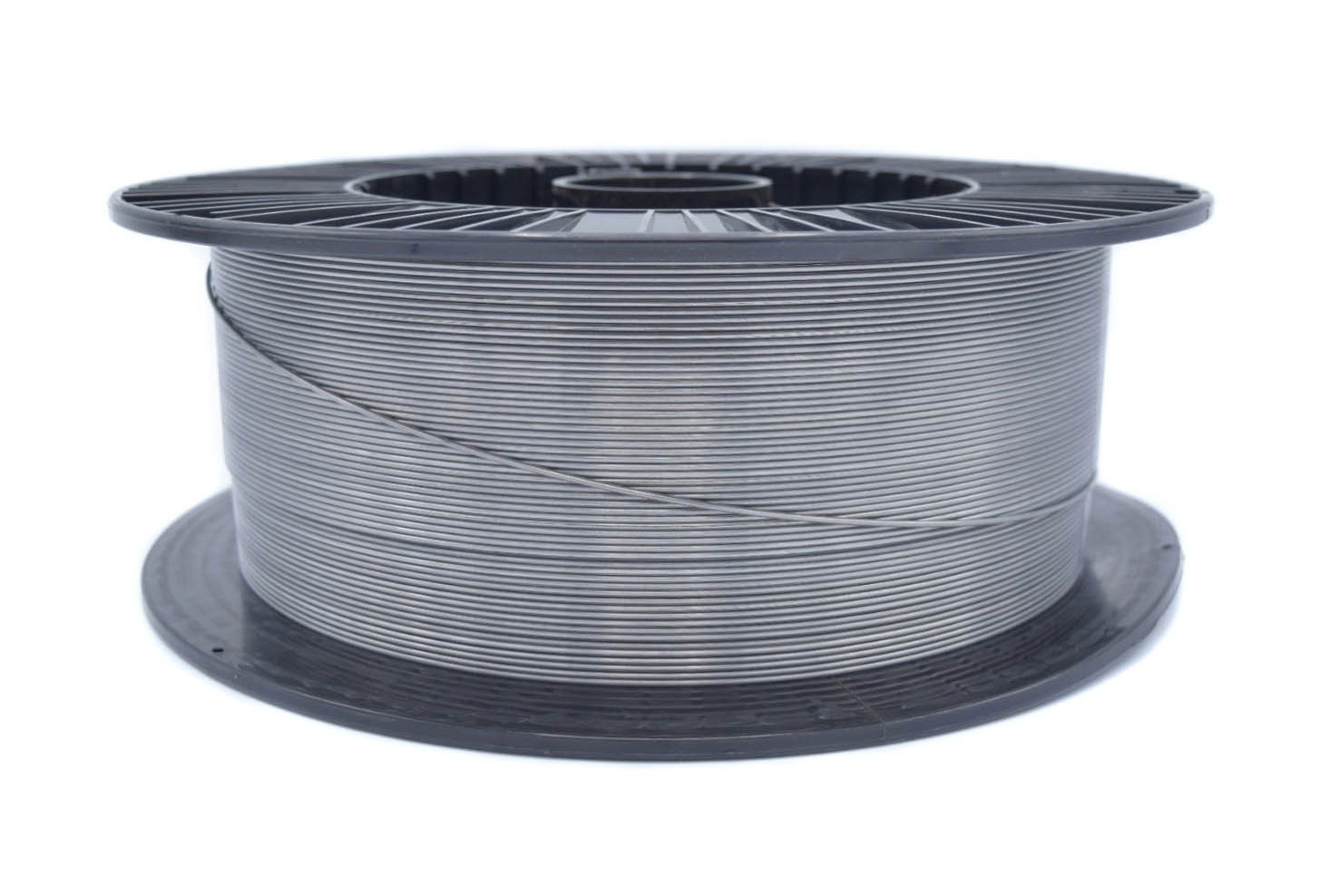
Technique
Spray guns used to apply coatings should be held approximately perpendicular to the surface of the work-piece and at an optimum distance to deposit a proper coating (typically 8 to 10 inches). Each pass should overlap approximately 50%. Bond strength is improved by keeping the coating passes thin. Excessively thick spray passes increase internal stresses in the coating and reduce bond strength. Apply the deposit by moving the gun head from side to side in order to maintain a consistent distance from the gun nozzle to the work piece. Fan spray air caps are available for both combustion and twin wire arc applicators which produce more of an oval shaped deposit pattern to aid in consistent deposit coverage.
Aluminum thermal sprayed coatings are typically sprayed to a total thickness of 15 mils (.38mm), with a minimum of 10 mils and maximum of 20 mils, although individual customer requirements may vary. In order to obtain the maximum cathodic protection that TSA coatings provide, it is important that all sprayed areas are coated to this thickness and not merely averaged. Coating should be masked approximately 1 to 1.5 inches (25 to 38mm) from any area that will receive a future weld so as to avoid interference with the welding process. These areas will need to be prepared and sprayed after final installation.
A wide variety of sealers and paints may be applied to the finished TSA coating per the customer’s specifications, however, a properly applied coating does not necessarily require sealing in order to provide protection. Sealed coatings are hard to touch up with the thermal spray process should testing reveal any defects, as the they will reduce the bond strength of any coating applied on top of the sealed area.
Quality Control of the Coating
Visual inspection
All coated surfaces should be visually inspected after the spraying process is complete. Defective or non-conforming coatings should be repaired in accordance with the following repair section. The coating should have a uniform appearance with no discoloration. It should be free of lumps, coarsely sprayed areas, blisters, cracks, chips, or loosely adhered particles. Many clients require that the coated areas be sprayed with industrial water and re-examined after 24 to 48 hours for any indication of rust blooms or “bleed-thru” to ensure the integrity of the coating.
Coating Thickness
After cooling, each coated component should be inspected and measured for proper thickness and the results recorded. Thickness on iron based alloys can be checked with any manual or digital magnetic film thickness gage. Non-Ferrous surfaces (stainless, etc.) may be checked with a Non-Ferrous DFT gage such as the Elcometer 6000 NF or equivalent. Non-conforming coatings should be marked with chalk and then repaired by the applicator. Gages should be calibrated using certified coating thickness calibration standards at the start of each shift they are used.
Adhesion Tests
A generally accepted adhesion test for TSA coatings consists of three separate pulls using three 1” (25mm) “dollies” similar to those used for ASTM C633 or ISO 4624 tests. These test cylinders are glued or epoxied to the aluminum coated component or preferably to a companion coupon that is prepared and sprayed at the same time the coating is applied. Once cured, the “dollies” are removed or pulled using an Elcometer 106/3 or equivalent tester. Adhesion values obtained should meet or exceed 1000 psi (500 psi for Zinc)
If adhesion measurements fall below the minimum value, three additional measurements should be made on the chosen component. One of the three should be in the vicinity of the failed test and the other two at random locations on the component. If these three additional measurements prove acceptable then the component is considered complete. If not, then additional testing may be required to obtain the scope of the defective coating area. Defective coatings should be removed by blasting and the spray process should be adjusted to correct the defective parameters and the test sample procedure repeated. Adhesion tests should be performed daily on each component or sample coupon for that component.
Bend Test
A bend test is a quick way to test for proper surface preparation, equipment set up and proper spray parameters. Using a carbon steel coupon that is approximately 2” x 8” x .050” and prepared with the same grit blasting as the component, coat the coupon with approximately 7 to 12 mils using the same thermal spray equipment and settings. Bend the coupon 1800 around a 1” (25mm) diameter mandrel. If the TSA was applied correctly and everything is functioning within normal parameters, there should be no cracking or spalling (or only minor cracking that cannot be lifted from the coupon with a knife). If the coating cracks and lifts from the substrate then the bend test is failed and spray parameters and surface preparation must be adjusted before proceeding. Bend tests should be performed for each sprayed component. Many customers require both a bend test and an adhesion pull test.
All quality control aspects of thermal spray coatings should be recorded for future inspection. In the case of on-site application, the owner’s inspector will want to be present when these tests are performed.
Repairs
Generally speaking, TSA coatings may be recoated within an 8 hour shift without any further surface preparation as long as the surface has not been contaminated or sealed. If the coating thickness is determined to be lacking in areas, these can simply be sprayed again. If the time period has exceeded 10 hours or if rust bloom occurs, the surface should be brush blasted (per SSPC-SP7) to remove any surface oxides that might have formed that would interfere with adhesion, and then the area may be recoated.
In the case of failed adhesion or bend tests, or any coating that is determined to be defective all the way to the substrate, the entire surface preparation procedure should be repeated (white metal blast) and TSA re-applied per specifications. All quality control tests should then be repeated.
Documentation
As indicated above, detailed records of the entire coating process should be maintained on some type of an “inspection report” including: ambient conditions for the day, wire certifications, blotter tests for air supply, abrasive cleanliness, anchor profile, steel temperature, coating thickness, material test results, TSA procedure used, labor hours, operator names and training certifications, and the results of any quality control tests performed. These records should be maintained for an indefinite period in digital form for possible future use. Non-conformance Reports should be prepared to document all significant variances and the subsequent corrective action along with any owner feedback or approvals.
References
This document was created from references to the following material and publications:
Published and Non-published TSA requirements from Shell Oil Company and Exxon/Mobil
ASTM B 833 Zinc and zinc alloy wire for thermal spraying (metalizing)
ASTM D 1186 Standard test methods for nondestructive measurement of dry film thickness
ASTM D 4285 Standard test method for indicating oil or water in compressed air
ASTM D 4417 Standard test methods for field measurement of surface profiles
ASTM D 4541 Standard test method for pull-off strength of coatings
SSPC-SP1 Solvent Cleaning
SSPC-SP 5/NACE #1 White Metal blast cleaning
SSPC-AB 1 Mineral and slag abrasives
SSPC-CS 23.00 Specification for the application of thermal spray coatings of aluminum and zinc
AWS C2.18 Guide for the protection of steel with thermal sprayed coatings of aluminum and zin
AWS C2.25/C2.25M Specification for thermal spray feedstock solid and composite wire
ISO 209-1 Wrought aluminum and aluminum alloy
ISO 2063 Thermal Spraying
ISO 2178 Non-magnetic coatings on magnetic substrates – Measurement of coating thickness
ISO 4624 Pull-off test for adhesion
ISO 8503-5 Preparation of steel substrate
ISO 14918 Thermal Spraying – Approval testing of thermal sprayers.